Earlier this year I made a Bowie knife where I was attempting to make it slightly larger than one had made previously and I wanted to try and get a mirror finish on the blade. It was made from 5160 spring steel flat stock that was 1/4″ x 1 1/5″. All the forging was done by hand using the charcoal forge. It took quite a while to get the shape hammered out.
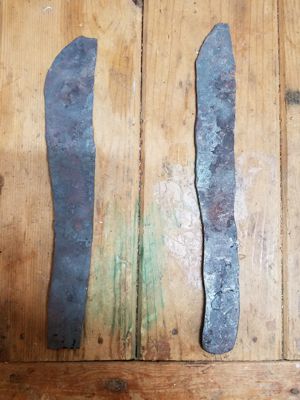
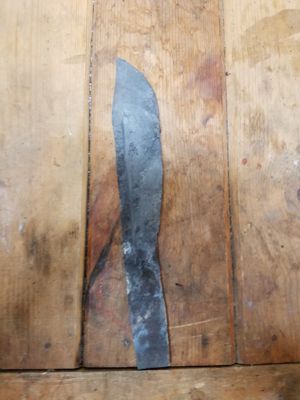

This knife was “ground” using the Harbor Freight 4″x36″ sander and it took a fair bit of effort to get it ground down even using 24 grit belts. After the heat treat I did more finish grinding and then installed a brass guard that was cut out of 2″x1/8″ brass stock. The scales were made of wormwood white oak that was dead fall on the homestead. In addition to milling dead fall into fence boards, I also make project boards that vary but are generally ~3/4″ x 6″ that I use for various projects.
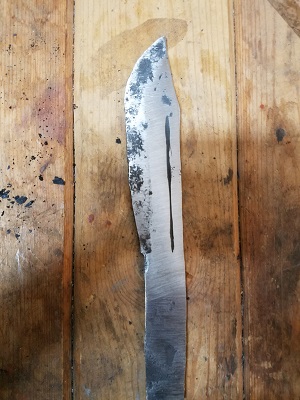
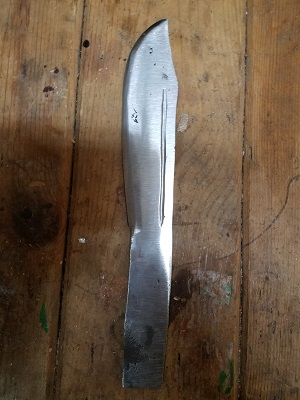
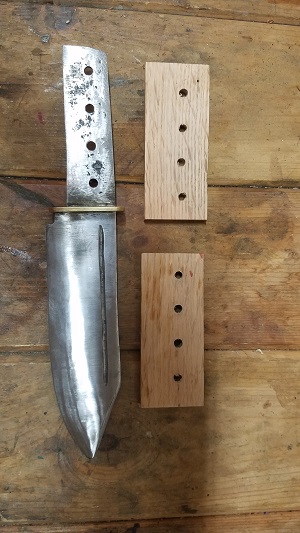
I have come to the conclusion that I do not like 5 minute epoxy. It sets up so quickly that if there is a little bit of an issue with a pin, or aligning clamps, all of the epoxy has to be removed. Since this project completed I am now using 15 minute epoxy and it works better overall for me. In addition I have found a 15 minute epoxy that has significantly less fumes/chemical smell. Its from Bob Smith Industries and is available on Amazon for around $12.


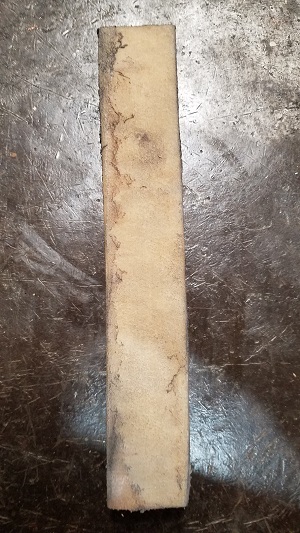
I am using 3/4″ and 1″ barrel sanding drums on a drill to grind the finger wells. It seems to work pretty well with the exception of the paper constantly clogging. Every few minutes I have to unclog the drum with a sanding eraser. They are also called sanding belt cleaners and are available from Harbor Freight or Amazon for under ten bucks for the 8″ long ones. Using a belt cleaner will definitely extend the life of your belts and drums but you cannot wait until they are totally clogged before cleaning them.
In order to get the mirror finish you have to grind to at least 800 grit. After that I used 1″ felt drums on a Dremel with polish compound. Care must be taken when using the Dremel because if any part of the tool rubs against the blade it will make a small scratch.
I originally put a poly coat over the blade except on the cutting edge to reduce corrosion. It worked fairly well but there were some small oxidization spots that appeared after a few months under the finish. I removed the poly and touched up the grinding and refinished it. Removing the poly was a pain and can cause fine grit belts to clog. I was able to remove some of the finish with paint thinner, but I need to figure out a better method in the future.
Update 11/16/2019 – This blade is up for sale on my Etsy shop here.