I have been working on blacksmithing and knifemaking for a couple of years. I started with a minimal investment and made the forge myself. A friend of mine had made a little forge using the rear break drum from a truck and had attached a piece of steel pipe that eventually transitioned to a PVC pipe. He was using charcoal for fuel and a hairdryer for air. His forge was held up by cinder blocks and he was using a railroad track joiner as an anvil. To keep the charcoal from falling down the pipe he used a couple of layers of stainless steel 1/2″ mesh.
I took his idea and made some improvements. I welded on an adapter flange that allows 2″ black pipe to be screwed in. A T about a foot down from the break drum allows air to come in and the ashes to fall to the bottom. A screw cap at the bottom holds the ashes up and allows the air to only flow upward into the forge. Using an old bed frame I made a stand that holds the forge and the squirrel cage fan. I used metal flexible hose to bring the air from the fan into the T. I bought a fan with variable speed control built in on Amazon. The break drum can be bought from automobile shops or junkyards for a few dollars.
In general this setup works pretty well, however the fan output doesn’t vary enough between the lowest and highest setting. I also wish the fan produced more airflow when turned up all the way.

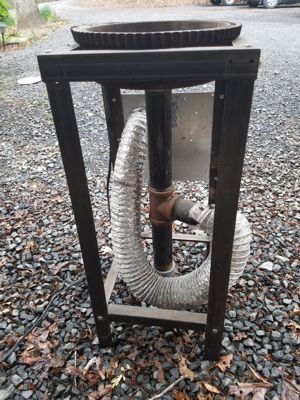

After using the forge for a while one issue was the stainless steel mesh holding up the charcoal clogs after a while and restricts airflow. To remedy this I took some 1/4″ square stock and built a circular “mesh” with about half inch gaps between the steel. This works much better and cleans out pretty easy since you can just take out the grill and bang it on something to clean out the debris and clinkers.
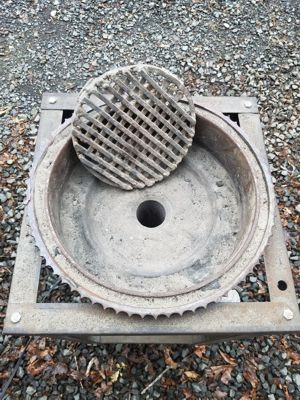
This setup definitely works, but it takes a while to get the charcoals up to temperature and heating the stock takes a while. Better airflow from the fan would help with both of those issues. A charcoal forge can reach temperatures of 1600 degrees Fahrenheit which is hot enough to do any forging except forge welds. A few other down sides is you will definitely smell like smoke and you have to dispose of the ashes fairly regularly. I found I could forge for about 2 hours but after that there were air flow restrictions from the ash and clinkers that greatly reduced the efficiency.
